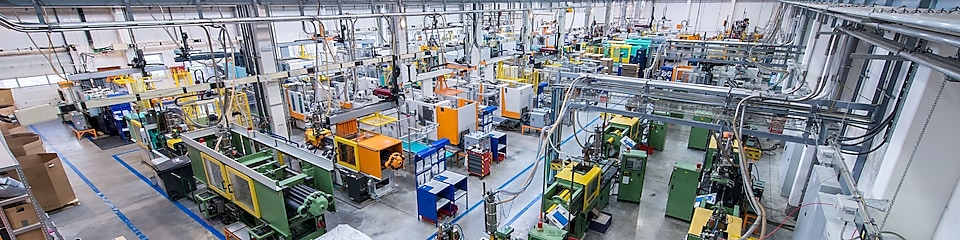
Overcome Production Challenges for Plastics Converters with these Output-Boosting Expert Tips
Meet consumer demands with our Polymer Pros and Polymer Pioneers
By Shell Polymers on Jun 25, 2020
When COVID-19 spread across the globe, polyethylene products such as medical equipment components, health and hygiene products, and food packaging were key to society’s response. Many plastics converters however, reported difficulties in accelerating the production of such orders without suffering a corresponding increase in machine downtime or product defects.
As film producers and injection molders are among those that have experienced an upsurge in demand, we asked Shell Polymers experts from these disciplines for tips that may help companies to debottleneck their lines.
Enhance Film Production with PPAs
For film producers, Dan Falla, a Senior Technical Service Engineer at Shell Polymers that specializes in PE film, suggests that companies consider using a polymer processing aid (PPA). His reasoning?
“PPAs reduce back-pressure and the motor load so they can help to raise output significantly, and also reduce downtime.”
Dan Falla
Additionally, effectively using polymer processing aids can have a major impact on a polyethylene film producer’s product quality and output. As a general rule of thumb, Falla says, 500–1,200 ppm of a polymer processing aid should enable an 8–15% increase in output, provided the operation is not constrained by other attributes such as winder speed, cooling, treating or the supply of resin to the feeder.
Another area to consider is the layer ratios and composition of multilayer film structures. “I’ve seen plastic converters unlock major increases in output rate by making adjustments here,” he says. If still producing monolayer films, plants can realize additional cost savings by producing multilayer films instead. The cost benefits come from being able to use less-expensive resins in the core and fewer additives, as they are only necessary in the skins.
Multilayer lines also enable film producers to create engineered films that have unique properties over a wider variety of widths and line speeds.
Of course, plastics converters should always be careful to avoid adding too much PPA. This negatively affects the film’s properties and increases production costs, which can impact the overall supply chain.
Improve Injection-Molded Part Quality
Plastic injection molding is one of the leading processes used for manufacturing plastic products. Its strength lies in its ability to produce identical parts rapidly with tight tolerances and a high-quality finish. As such, ensuring part quality is critical to success as a plastics converter that works in injection molding.
Elliot Carnevale, Technical Service Engineer - Injection Molding, advises that businesses should continue to ensure adequate cooling and pack time when trying to achieve faster cycle times.
“Faster cycle times often mean less cooling, and if a part is not getting the same amount of cooling as it has historically, molded in stresses, or part design issues can lead to warpage,” he explains. “Alternatively, faster cycle times can lead to parts being packed out insufficiently, which would manifest as sink marks. When it comes to part quality, fractions of a second in these areas can make a major difference.”
Ultimately, Elliot explains that defects aren’t usually caused by a single problem. It is a common practice for plastic converters to hunt for a single solution and, when you find it, assume that will solve all your problems in the future.
“Defects and processing issues are usually the result of multiple variables combining to cause a problem.”
Elliot Carnevale
Working closely with a knowledgeable polyethylene supplier, take a fundamental approach to problem solving and looking at the part design, mold design, process and material will provide a list of possible variables driving the issue.
With over 750+ collective years of experience, Dan, Elliot, and the other Polymer Pioneers and Polymer Pros can offer useful insights at this time of need. Connect with one of our team members to brainstorm innovative ways of increasing output.
Learn More About Polymer Technology